The new PC-based marking controller LUCy is the control basis for all marking machines and is capable of controlling up to four axes (X,Y,Z,A) simultaneously. The marking controller can be used as a desktop controller or for control cabinet mounting, and is combined in a space-saving housing. It has a 10.1″ touch display for visualization. Interfaces: 1x RJ45, 2x USB ports for keyboard, mouse or barcode scanner, HDMI.
The marking programs are created and managed with the LUCy G2.0 software. When creating the marking layout, you always keep an eye on the essentials. The LUCy G2.0 software creates G-Code files (DIN 66025/ISO 6983) based on preset parameters and variables. The lines and arcs of individual characters are scaled, transformed and rotated using mathematical calculations. The resulting values are displayed as graphics in the software interface (marker preview) and used to create G-Code files. Additionally, modules for an automated generation of marker texts have been integrated. The software is network-compatible and can interact as master/slave.
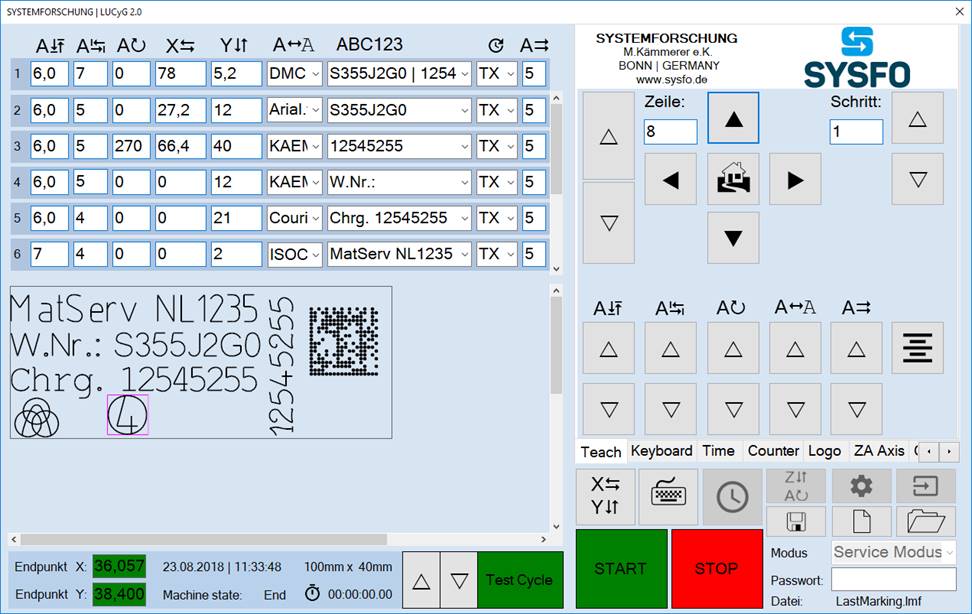
The components to be marked are positioned in an embossing press using robots in a hot forming system. In three steps, the embossing plant embosses the manufacturer’s symbol and the supplier code, part number and revision status and the production date in less than 3 seconds. Depending on the version, data matrix codes can be marked via the free X and Y axes. The engravings are designed in such a way that they do not damage the applied aluminium oxide layer.
The selection and positions of the wheels are monitored by incremental encoders. For this purpose, the specially developed “Close-Close Loop” method is used, in which the control system compares steps and step losses and readjusts steps if necessary. If the desired positions can no longer be reached, the controller goes into alarm or malfunction mode before the marking test.
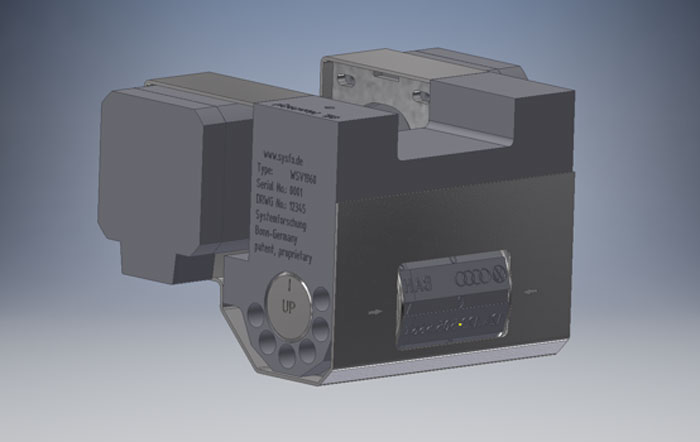
On the flame-cut surface of billets (marking temperature approx. 900°C), the batch number is stamped as plain text and a data matrix code using a needle marker. Marking takes place directly on the first station of the reversible cooling bed to avoid mix-ups. The markings are then read and verified with an OCR reading system. In the subsequent production steps (wire drawing, rolling mill), the marking is used for alloy or batch allocation. punch reading.
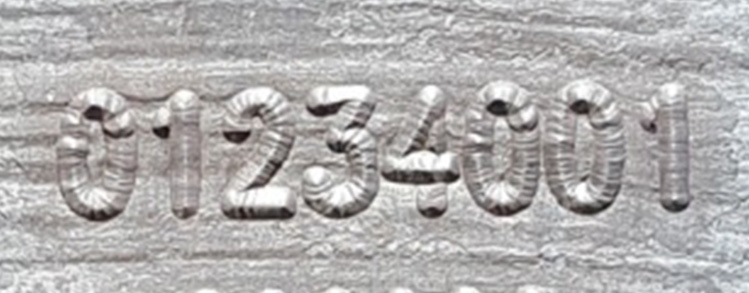
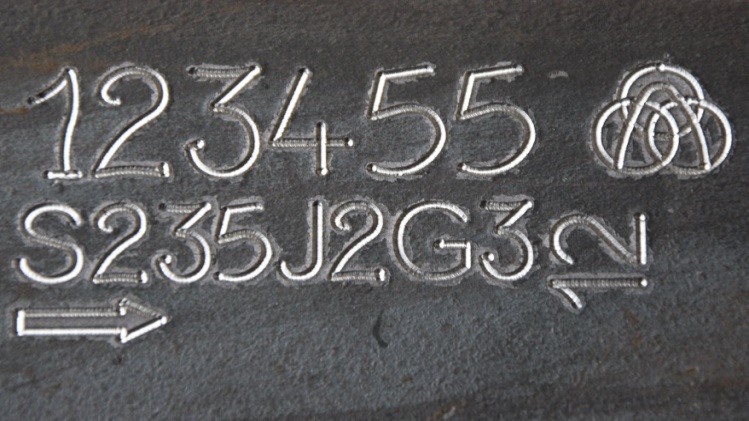
In the first step, the material samples supplied by the steelworks are marked at different positions before processing (saw cutting). From these, so-called “test specimens” (tensile torsion specimens) are produced in subsequent production steps. The markes numbers are marked with the font SysFont and are identifiable even if a part of the marking is missing or lost.
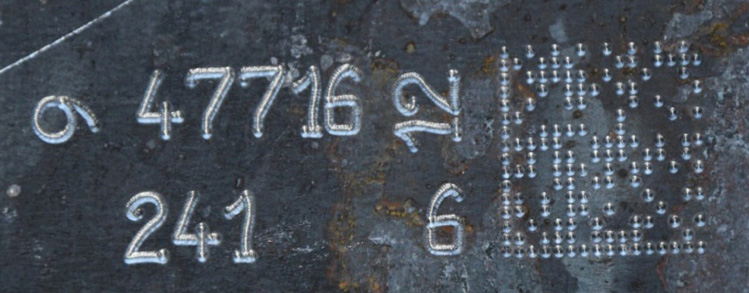
The markers show the difference between a marker in continuous vibration mode and a dotted marker. Both markings correspond to the so-called standard for pressure vessels (DIN, ASME, and AISI) in the “Low Stress” range (lowest notch effect), since the points were introduced into the component surface by means of a rounded needle. Due to its chemical composition, the needle does not produce any contact corrosion.
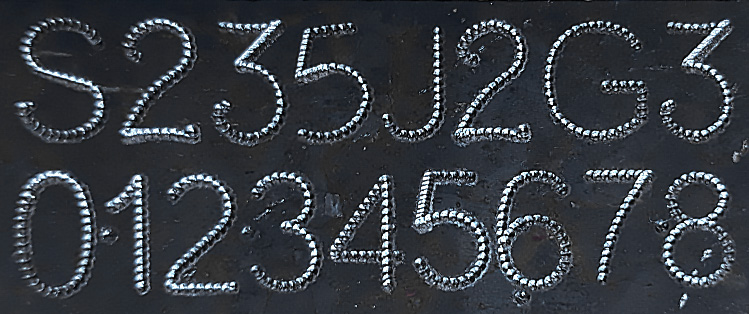
X40
Small, very fast, universally applicable marking units.
Versions: Mobile device, integration, table machine
Marking range: 50x40mm, 100x40mm, 150x40mm
Marking speed: up to 12 characters/sec*.
Dimensions (Integration Model) from: 105x180x105mm [bxhxt]
Weight (Integration Model): 1.7kg, 2.2kg, 2.7kg
Marking cylinder: V12/75, V16/75, V22/75
Marking depth: 0,05 -0,5mm (steel with a tensile strength of 520N/mm²)
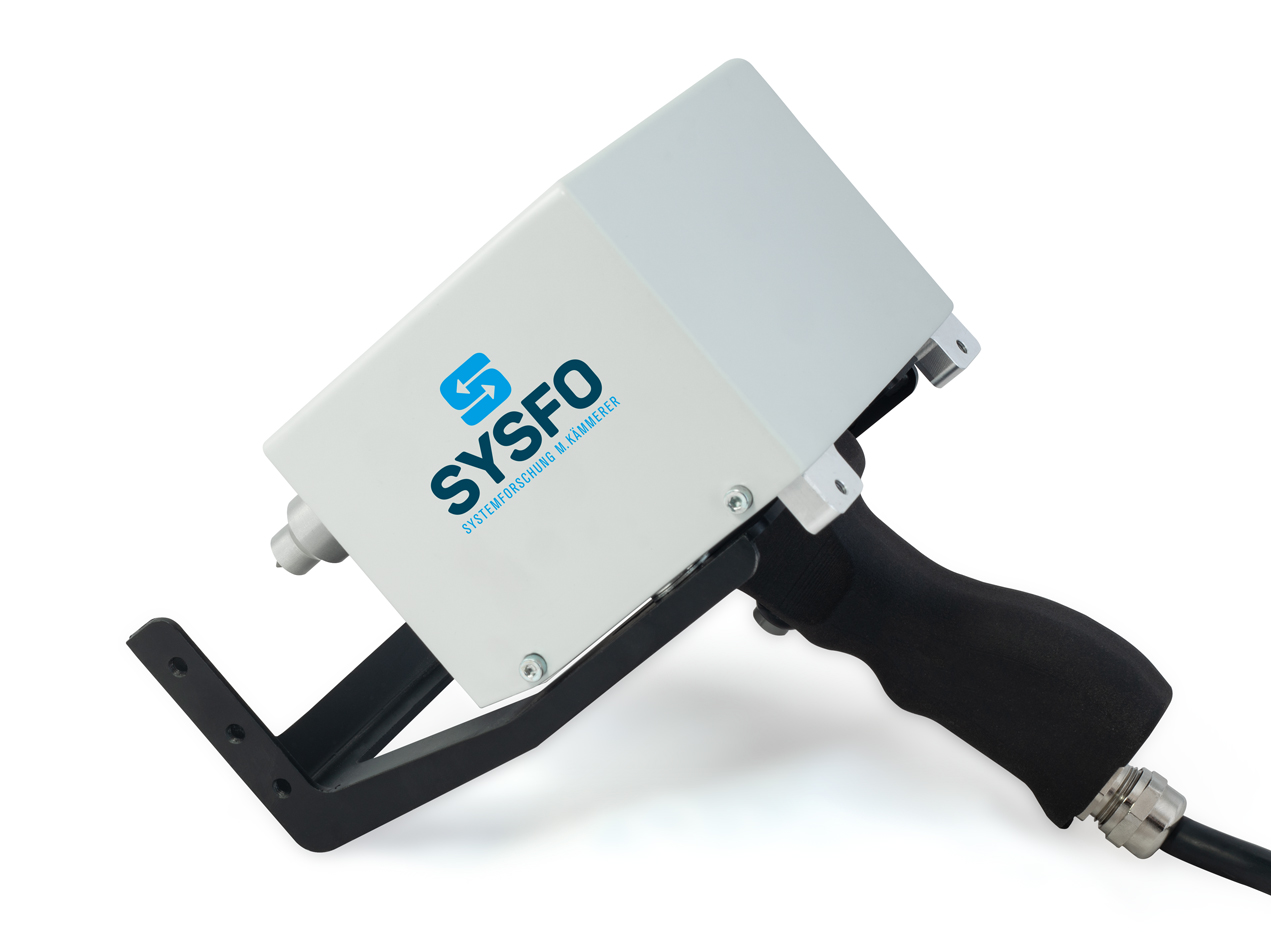