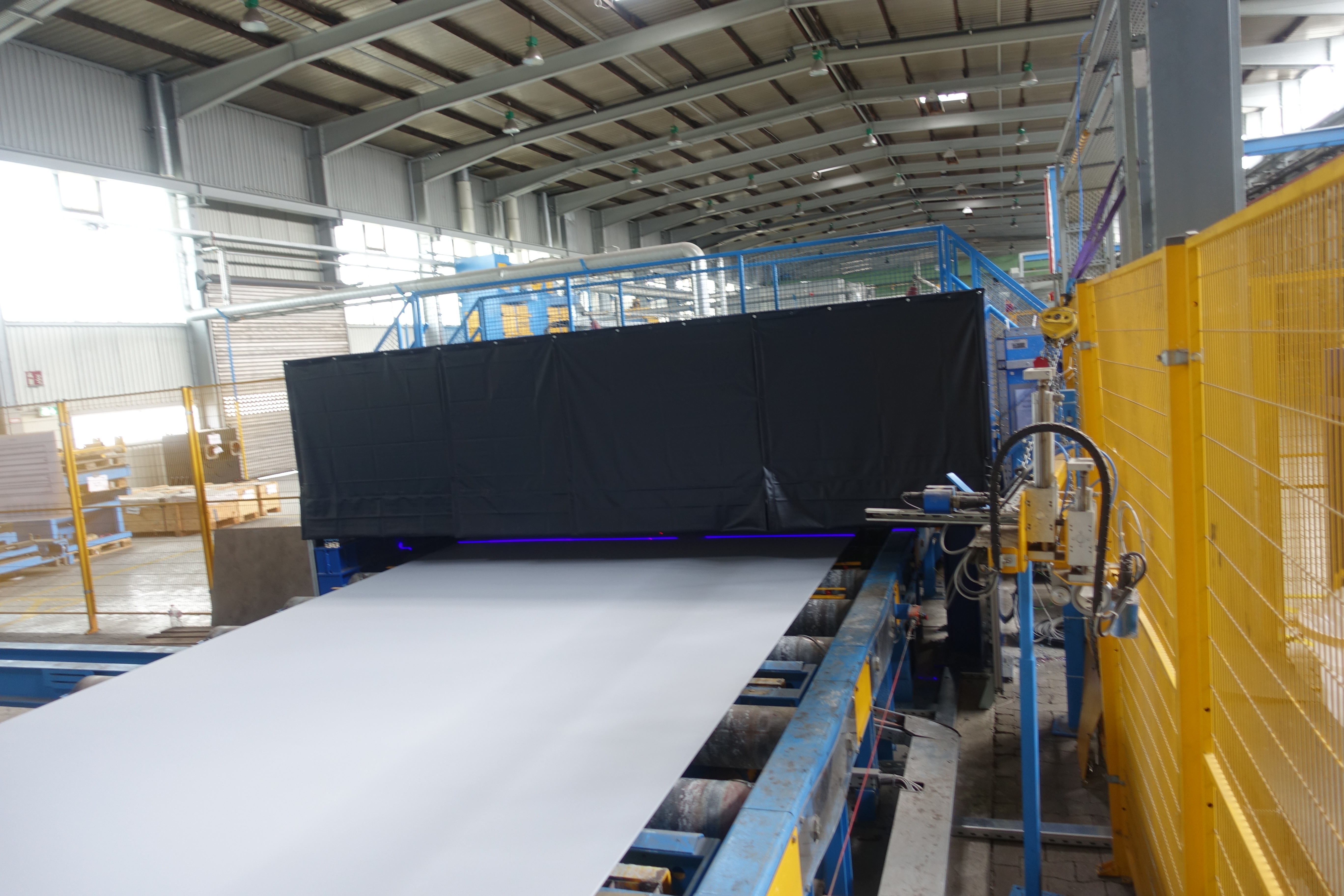
Side view: The camera creates 1000 3D profiles per second while passing through.
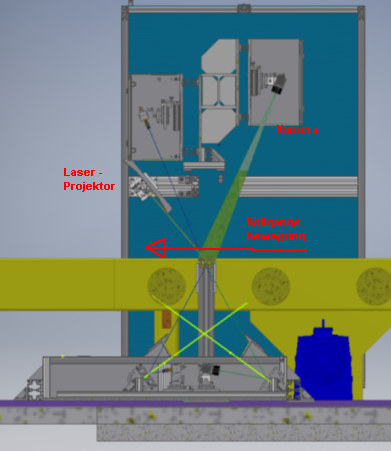
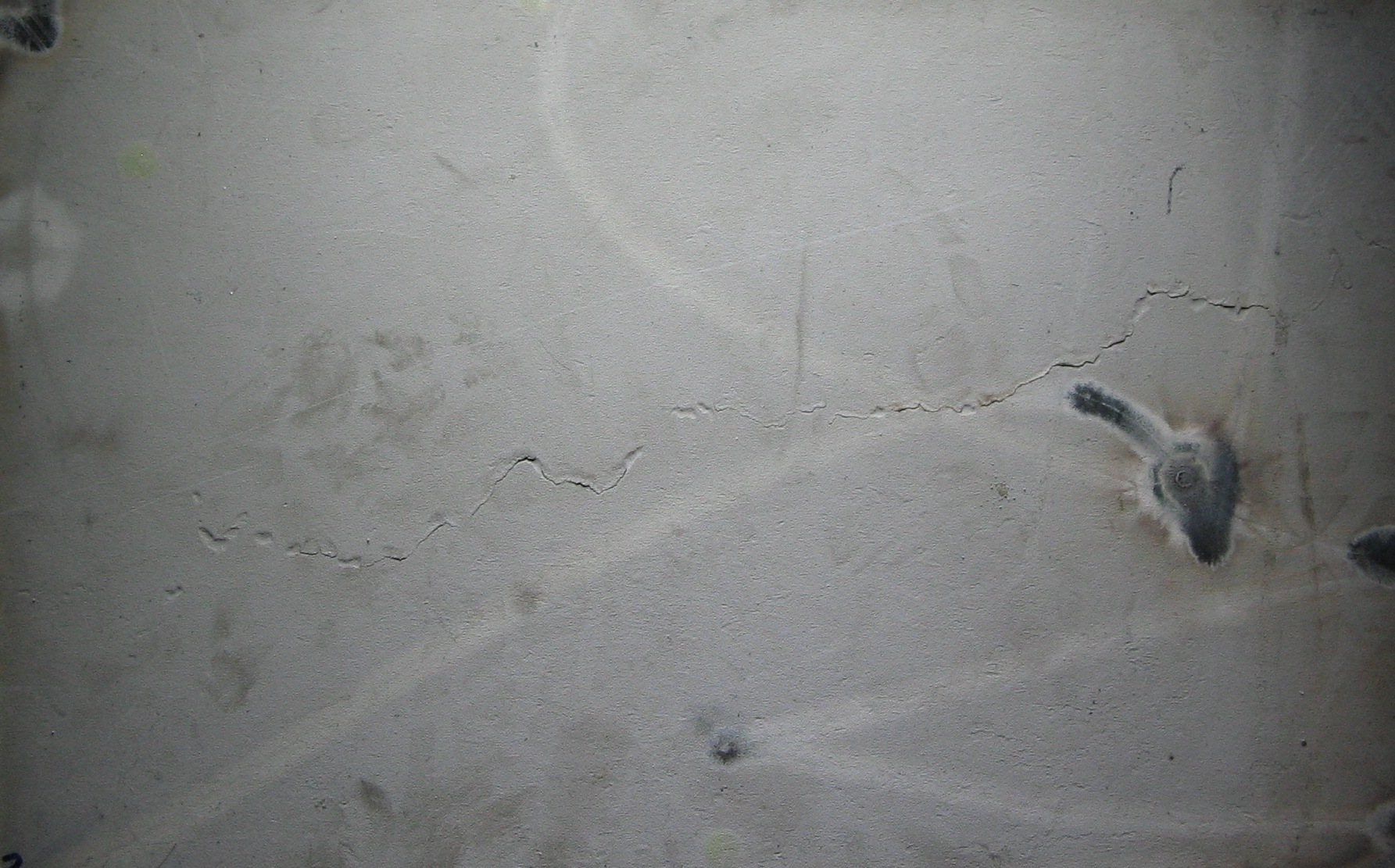
Evaluated 3D image
Grey: sheet level
White: at least 0.15mm raised
Black: at least 0,15mm deepened
The discolorations have no influence on the 3D image.
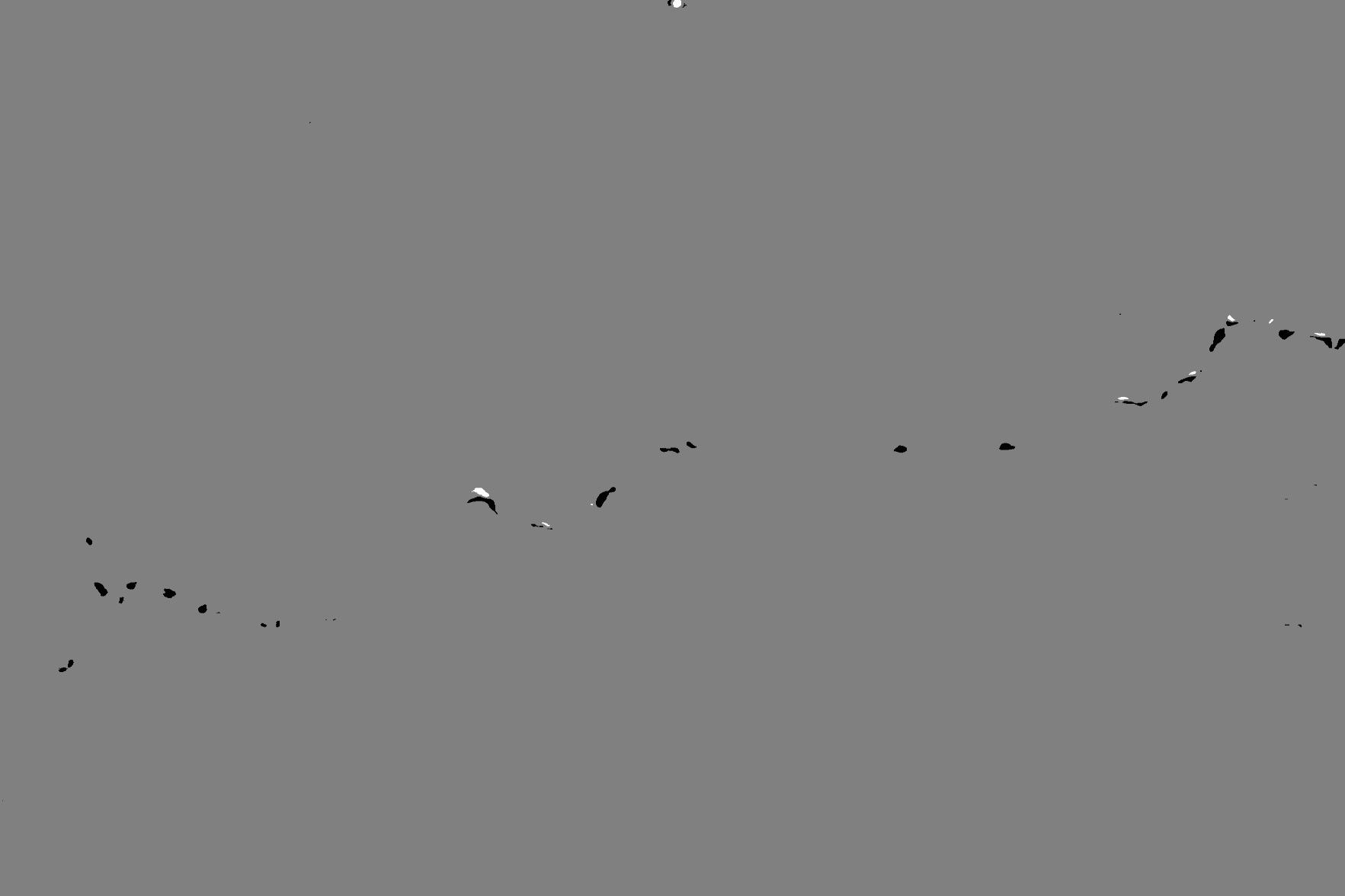
Side view: The camera creates 1000 3D profiles per second while passing through.
Evaluated 3D image
Grey: sheet level
White: at least 0.15mm raised
Black: at least 0,15mm deepened
The discolorations have no influence on the 3D image.