For crack tests on ferromagnetic steel parts in the aerospace or automotive industry, the crack indicators can be reinforced by flux testing (magnetic particle testing, for example according to DIN EN 10228-1).
The test piece is magnetized and then fluorescent magnetic powder (dry flux) or a suspension (wet flux) is applied. Under the magnetic field, the magnetic particles nest on cracks and are held there. Under UV lighting, the particles fluoresce and show sharp-edged cracks. A short exposure under current is sufficient and the evaluation can be documented permanently. The test medium is then immediately blown off and recycled, significantly reducing consumption.
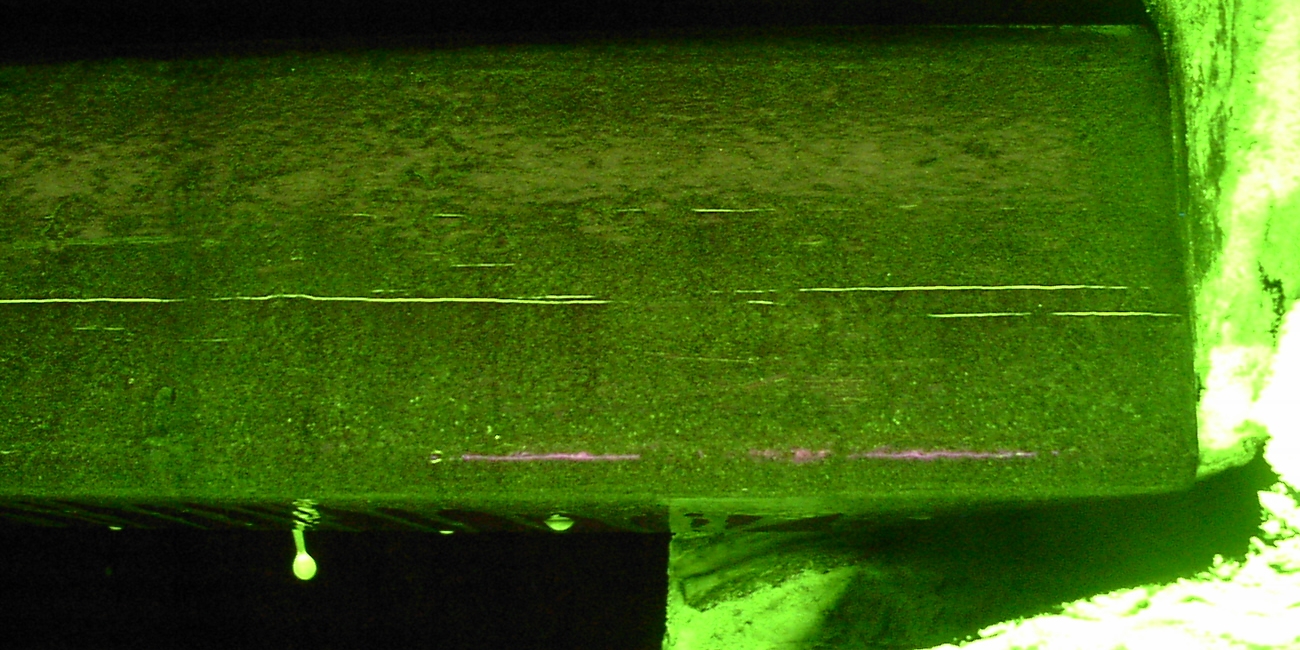
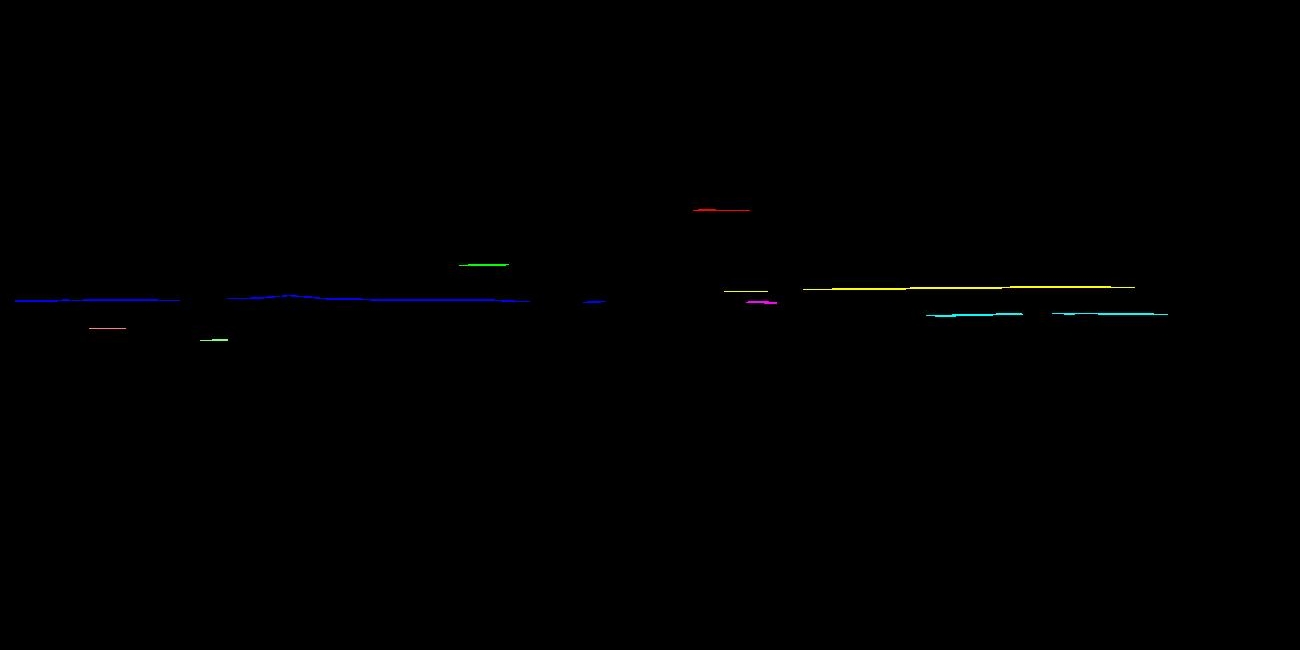
Even on complicated surfaces, such as here on a crankshaft, cracks can be indicated and detected automatically.
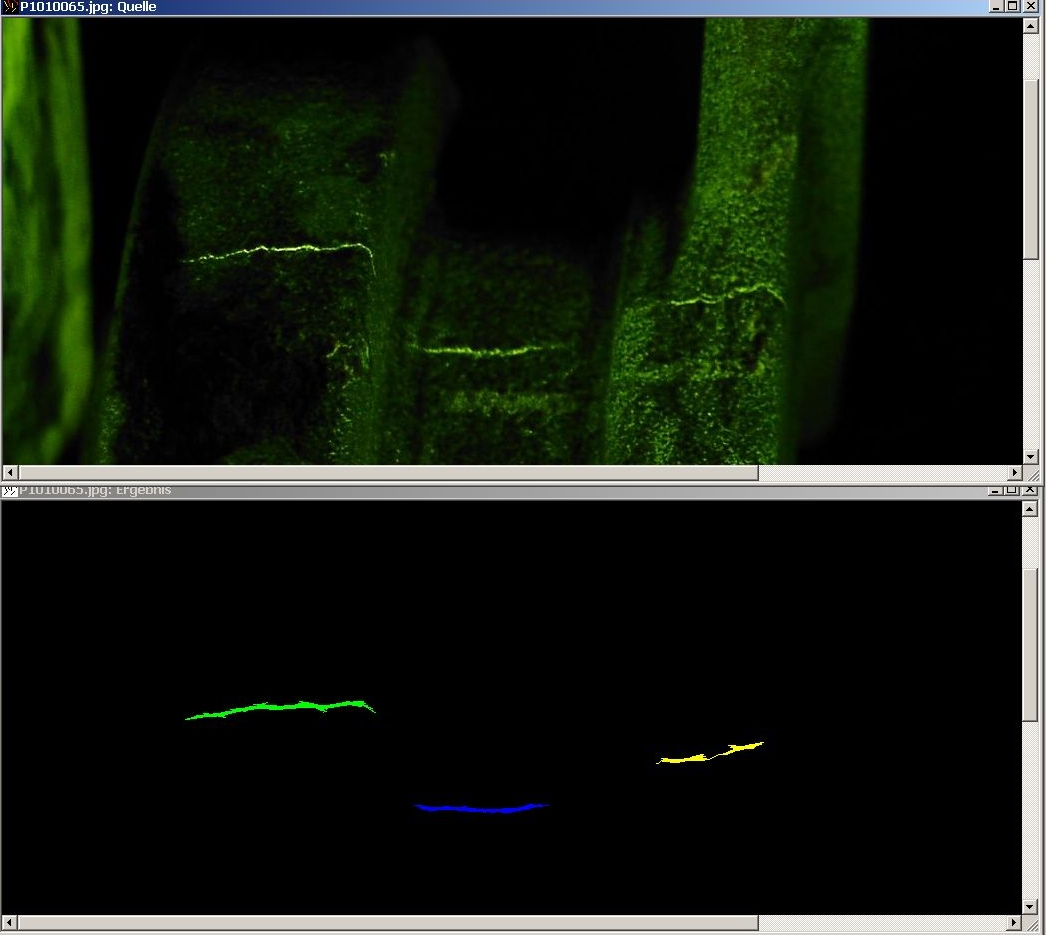