Mechanical design
The chain conveyor of the test line is covered by a measuring chamber, to protect the measuring equipment from external dust, temperature and light influences. Inlet and outlet openings are protected with strip doors. In the test chamber, a hydraulic cylinder with chuck lifts out the wheel lying on the chain conveyor and rotates it 360° around the wheel axis.
During the rotation, 4 high-resolution 3D laser scanners record a solid model of the surface. This measurement is repeated in a second rotation with an offset chuck so that the gripper positions do not leave any uninspected areas. The wheel is then lowered back onto the chain conveyor and released for further transport.
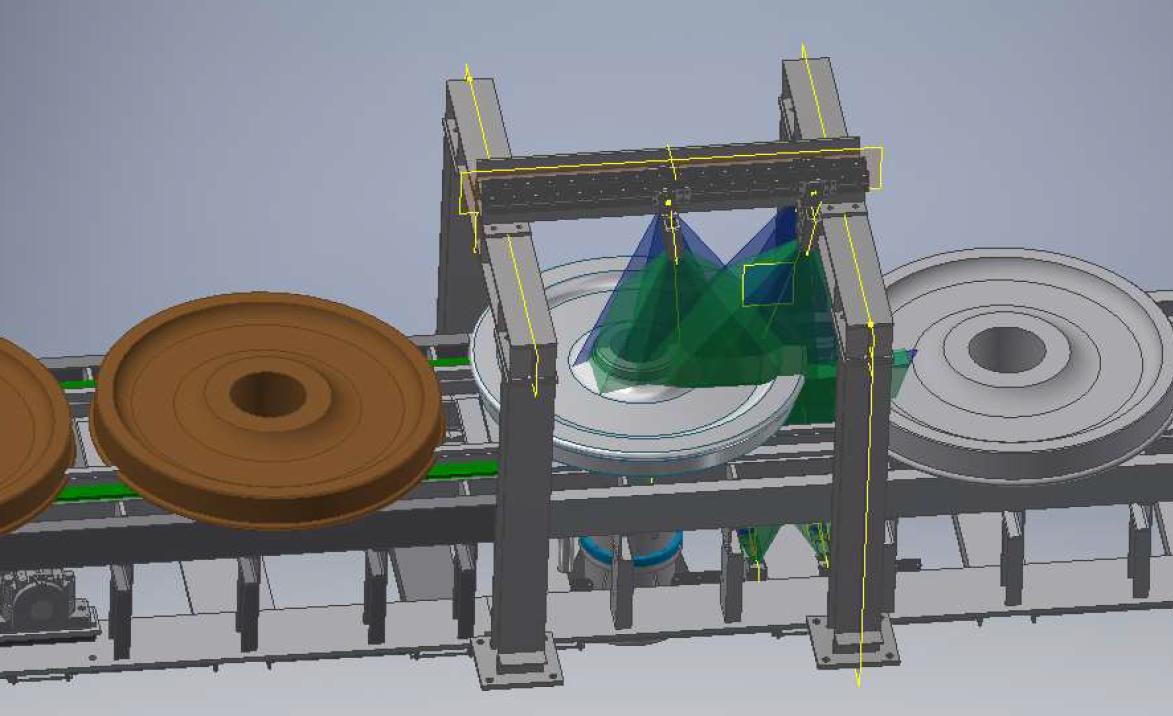
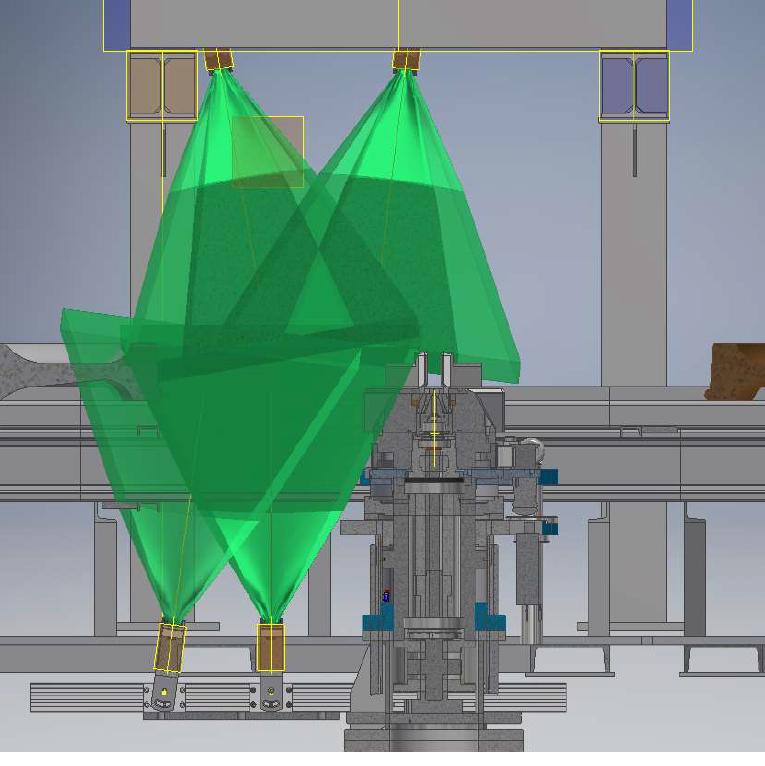
Before the test begins, the system receives the wheel type and the enable signal from the higher-level control of the test line when the test specimen is in position. The wheel is then lifted out of the chain conveyor, rotated and the angle tracked by a rotary encoder. The wheel is then lowered onto the conveyor, the chuck is rotated by 60° and in a second run the previously hidden areas of the underside are now visible.
During the 360° rotation, each camera generates a 3D model from approx. 3000 scans of the unwound surface from its perspective. The data are sufficient to effectively reduce the unavoidable measurement noise so that valid measurements on the model are possible. The cameras are aligned in such a way that, for each wheel size, all areas of the cross section are captured by at least one camera with a favorable viewing angle.
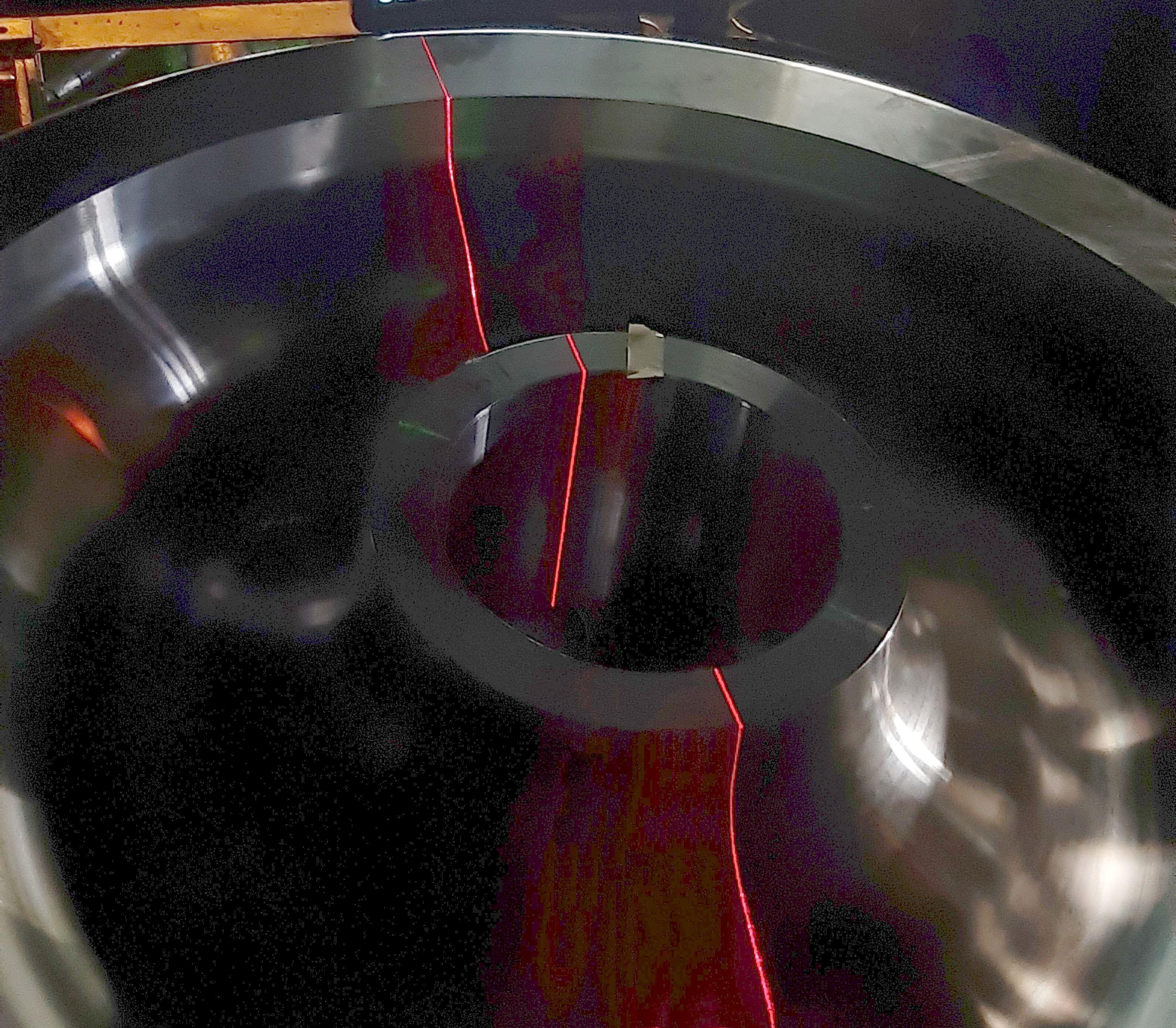
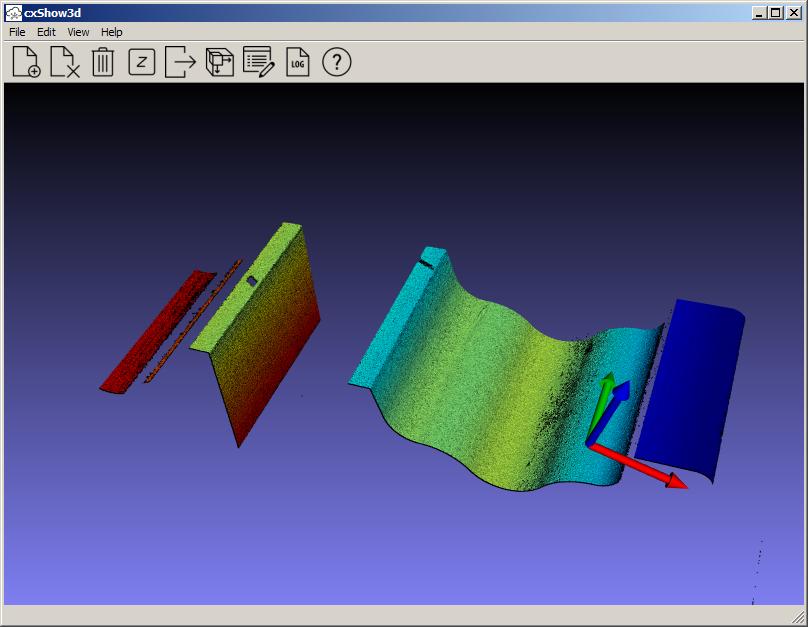
Section through a wheel side after the first turning process. The drawing is highlighted in gray and the measuring points from four perspectives are superimposed in different colors. You can see that the wheel still has oversize, as material is still required for the subsequent fine machining.
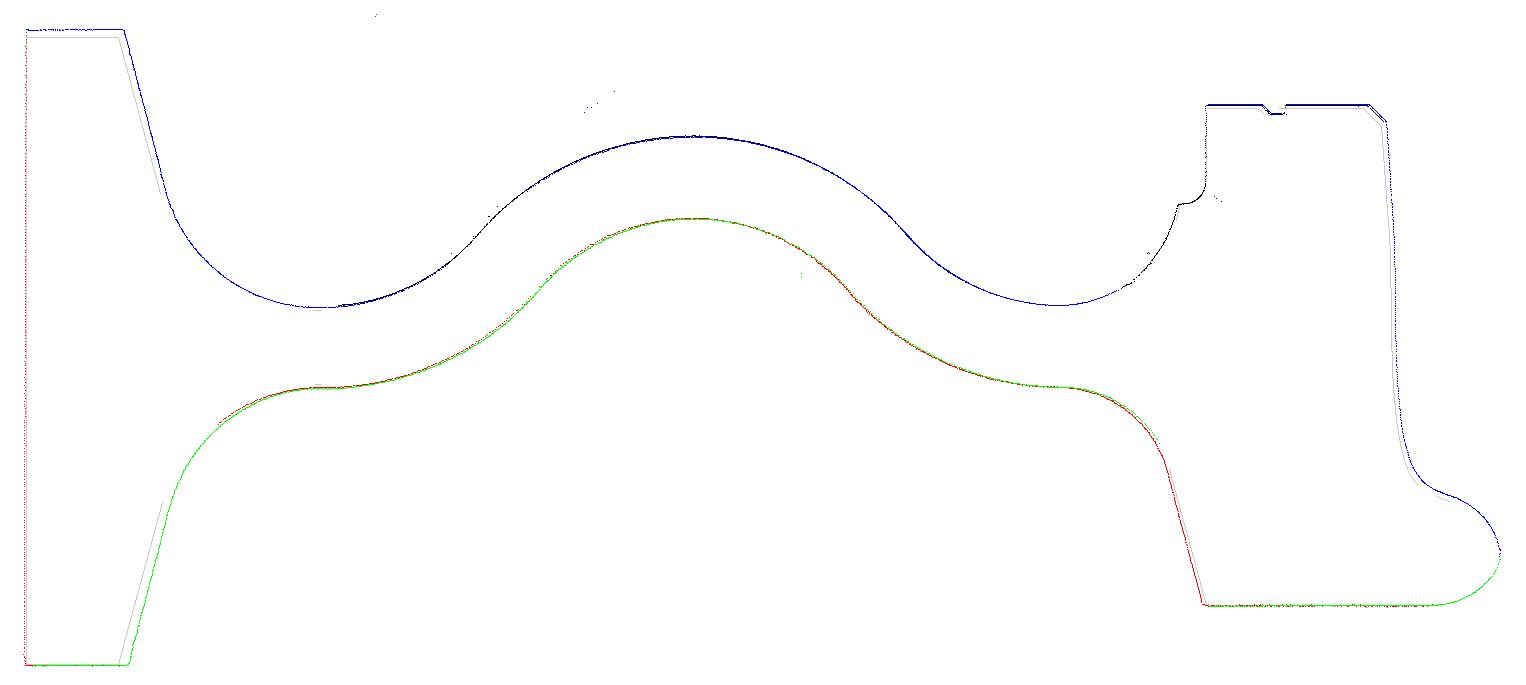
The Software is ready to install on WIN7 and Win10 PC (OS WIN7, WIN10 supported)
In the WheelDataResearchCenter overviews in tabular form, statistical evaluations and sectional views can be retrieved on the terminal and are available as printouts for retrieval. All data is stored on a central database server and compared with data from an existing material flow system and integrated into it. This means that statistics are also available on specific shifts, batches, and customers, so that transparency can be created at any time about the quality in the production process and weak points in production can be quickly detected.
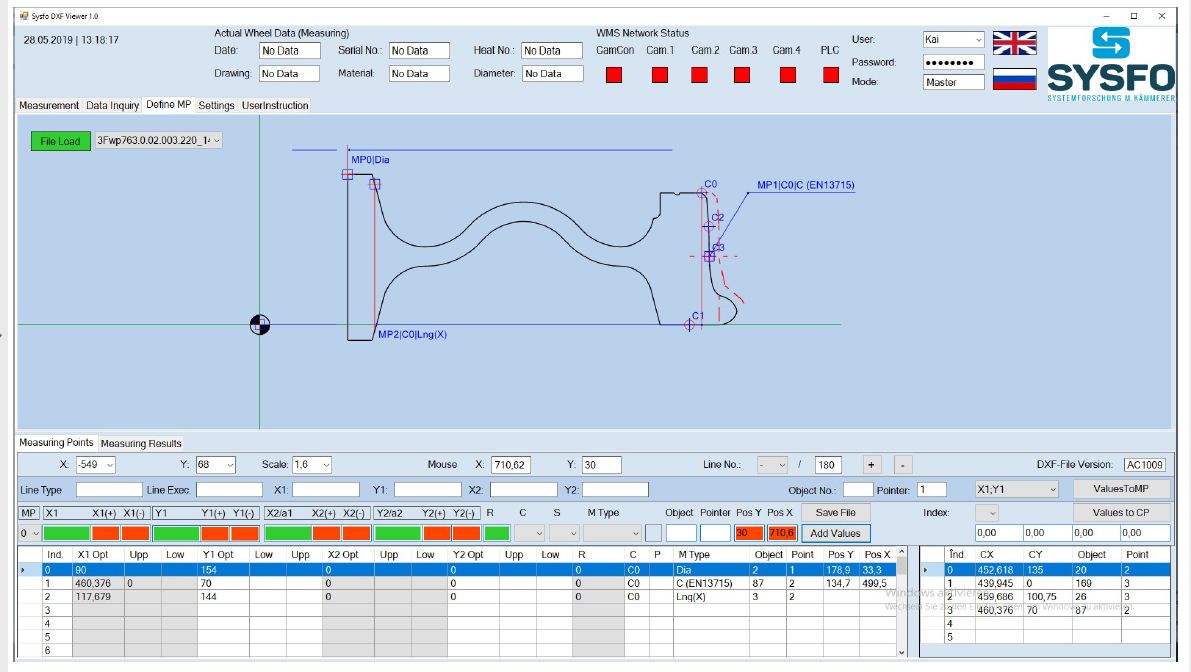
The light-section method allows reliable, precise depth measurements and contour checks by mathematical evaluation of the image data’s. This non-contact optical measurement system (laser triangulation) also is used for a high-resolution 3D axis inspection.
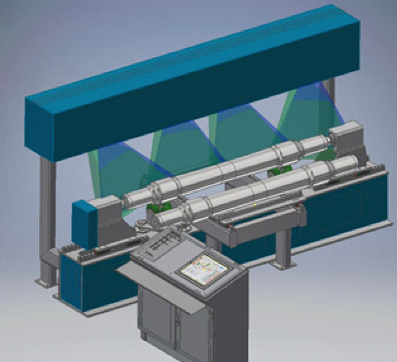
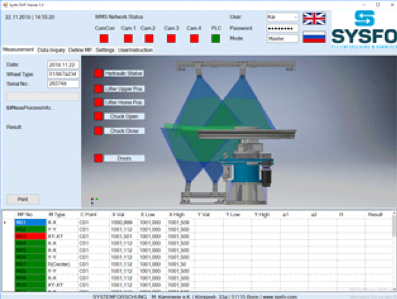
Furthermore the laser triangulation technology is able to evaluate complete assembled wheel sets in a roller prism.
Mit einer niedrigeren Kameraposition ist es auch möglich, Radsätze zu untersuchen, die in einem Eisenbahnwagen montiert sind. Insbesondere der Verschleiß der Lauffläche kann auf diese Weise überwacht werden.
For both wheels, synchronism, cylindricity, radial runout, lateral runout and contour shape are evaluated within one rotation.
With a lower camera position it will also be possible to supervise wheel sets munted in a railroad car. Especially the wear of the tread can be monitored in this way.
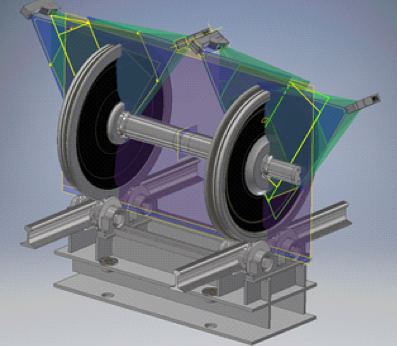